Glassware
11 min readGlass was called “Bi-Liu-Li,” “Liu-Li” or “Po-Li” in ancient China, and “Liao-Qi”in modern China. It has evolved into a form of art in contemporary China. Glassware in ancient China has vivid colors, and thin and fragile texture. Although western glass -making formula and techniques were introduced to China for several times, the intrinsic style of glassware in China remains unchanged. Modern glass art combines new materials with new techniques, and echoes with traditional Chinese culture. It has become an important part of contemporary Chinese art. Chinese people began to produce glass containing lead and barium in Western Zhou Dynasty. This kind of glass is different from the soda-lime glass in western countries. It is also different from the high-temper-, transparent glass of the Spring and Autumn Period and the Warring States Period. At that time, the lead -barium glass was made under low firing temperature. It has vivid colors, crystal-clear and brilliant appearance, but it is thin and fragile, has poor transparency, and is not accustomed to the sudden rise and drop of temperature. For this reason, it is unsuitable for making utensils, but is suitable for making ornaments, sacrificial vessels and burial objects. Its scope of application is narrow. In western countries, people began to make glassware earlier than Chinese people did. The western people also developed more advanced crafts of making glassware. Before the reign of Emperor Kangxi of Qing Dynasty, most high-grade glassware in China was imported from western countries.Glass beads of the Warring States Period(475-221 BC), kept in Hubei Provincial Museum. One strand of beads is in violet brown, of smooth surface and in regular shape. The other strand is composed of irregularoblate beads in light blue or green decorated with white or dark blue ringers, thus, commonly known as ‘dragonfly-eyed glass beads.Ear pendants of the Western Han Dynasty, 2.4cm in height, kept in the Palace Museum in Beijing.
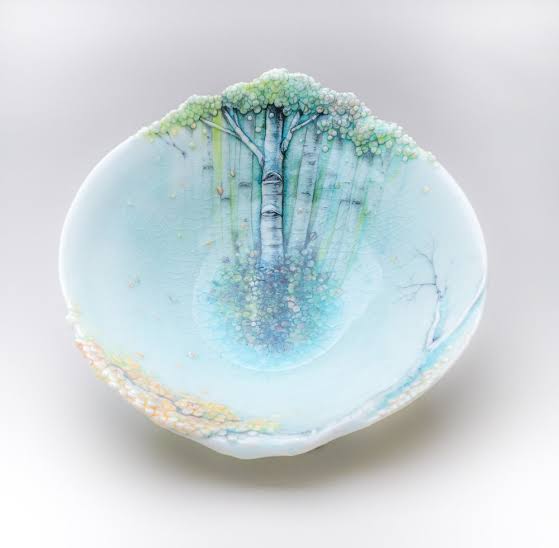
The pendants, translucent and dark blue, used to be quite popular in the Eastern Han DynastyGlassware-making techniques grew more mature in the Spring and Autumn Period and Eastern-Western technological exchange began at that time. Glassware-making crafts include casting, winding and inlaying. Glassware like jade disc, jade ring and sword ornament was made by pouring glass liquid into the mould. In late Spring and Autumn Period and early Warring States Period, “Dragonfly’s Eye” glass and imitated jade glass appeared in China. The base of “Dragonfly’s Eye”glass was made with the winding craft. Stick multi-color rings on glass beads, and create blue dots and light -colored (e.g. white)concentric circles on the glass. This glass was named “dragonfly’s eyes,”because its appearance is similar to the shape of dragonfly eyes. Similar glassware could be found in Europe, Central Asia, Western Asia and North Africa. This is common category of glass in the East and West. At that time, most single-colored glass was self-made lead-barium glass. Enamel alms bowl of the Northern Wei Dynasty.9cm in height, kept in Hebei Institute of Cultural Relics. The bowl is produced with transparent cyan blue glass by learning from the Roman Sasanian glassblowing method without a model, which had never been applied before the Northern Wei Dynasty in China. Enamel cannikin with a lid of the Sui Dynasty, 4.3cm in height and 2.8cm in diameter, kept in the NationalMuseum of China (formerly the National Museum of Chinese History). The cannikin is made of green glassand round-shaped, with a flat mouth, retracted head, round bottom, and an oblate lid. It is elegantly designed and looks crystal clear. Exchanges between the East and the West became more frequently in Qin Dynasty Han Dynasty and Southern and Northern Dynasties. China imported a large quantity of glassware from Roman Empire and Persia. In Han Dynasty, there were three production bases of glassware in China In Central China, craftsmen used crafts of Zhou Dynasty to make lead-barium glass; in Hexi Corridor regions, craftsmen used thetraditional formula to make lead-barium glass, and used soda-lime as the fluxing agent; Guangzhou was the glassware-making center in South China. It mainly produced potassium-silica glass. Glassware in Han Dynasty includes bowls, discs, beads earplugs and belt hooks, and has vivid colors, such as cyanic, blue, red, green, purple, yellow, black and white. In Wei and Jin Dynasties and Southern and Northern Dynasties, the locality separatist powers were keen on importing foreign glassware. Particularly in the Northern Dynasty, the locality separatist powers not only imported glassware, but also western glassware-making crafts such as the traditional glass blowing technique of Roman Empire. Since then, glassware became more popular in China, but it was not as precious as before. In Sui Dynasty, China ended its separatist status and was unified again. However, the firing glass-making craft passed on to China by businessmen fromDa-rou -Zhi- nation was lost. He Chou, famous craftsman in Sui Dynasty, succeeded in making translucent glassware by using the methods of making green porcelain. The light-green translucent glassware was similar to the green porcelain in North China. Few glassware of Tang Dynasty has been excavated by archeologists. Most glassware was made of high-lead glass without barium. Some glassware was made of lead glass containing sodium. For example, the glass fruits and glass bottles, which were excavated from tomb of Tang Dynasty in Lintong of Shaanxi Province, have traditional Chinese style, but they were made with the blowing craft of western countries. The glass fruits in light yellow and light green have extremely thin wall and were made with sophisticated techniques. In Tang Dynasty and Song Dynasty, glass being made in North-west China and coastal areas usually contains potassium and sodium. Potassium-lead glass has some merits. For example, it has vivid colors and light, fragile texture, but it can not resist high temperature. Therefore, this kind of glass is unsuitable for making tableware, but is suitable for making display articles and ornaments. People in Song Dynasty were particularly fond of glassware being produced in Arabian countries, because it is smooth, without cracks and can resist the high temperature in summer and the low temperature in winter. Glass-making industry was highly developed in Southern Song Dynasty. Suzhou and Xin’an were important production bases of glassware. In Hangzhou, the glass lamps being used on the Lantern Festival had vivid and brilliant colors. The glass-making crafts further developed in Yuan Dynasty. The government established “Guan-Yu-Ju,” a government-run workshop and regulatory body for making “Guan-Zi-Yu.” which was also called “Yao-Yu. This kind of glassware was made by imitating jade. The category of glass grew more diversified in Ming Dynasty and Qing Dynasty.
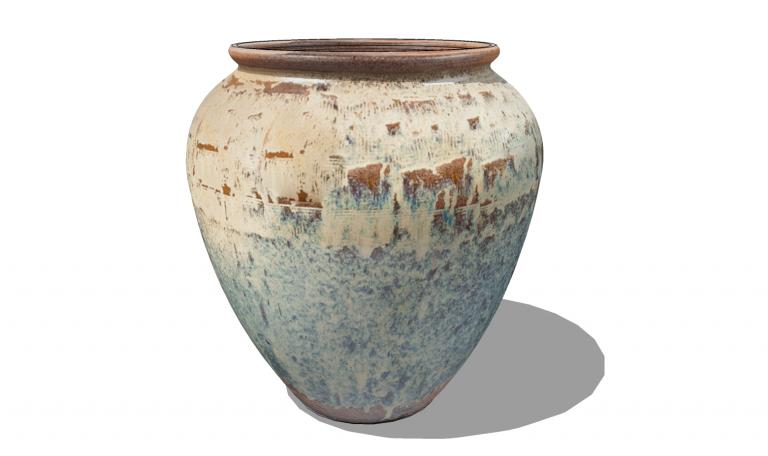
In Ming Dynasty, Yanshen Town (an ancient town in late Yuan Dynasty; now it is Yidu in Shandong Province) was an important production base of glass. Now on the ruins of the glass production site, archaeologists excavated glass-making furnaces, glass raw materials, glass fibers and glassware. Both the government-run workshops and privately-owned workshops could be found in the town. The government-run workshops mainly produce “Qing-Lian” (curtains made by blue glass sticks). The privately-owned workshops make hairpins and glass beads. They have vivid colors. Some of them are transparent, and others are not. ① White and blue enameled glass censer with knobs of the Qing Dynasty, 18cm in height, kept in the Palace Museum in Beijing. The body is in opaque white while the knobs (s-shaped handles) and animal-shaped legs are in blue.② Marbled enamel vase of the Qing Dynasty, 20.8cm in height, kept in the Palace Museum in Beijing. The unique patterns on the vase are produced by the complicated marbled technique. In the first place, the white clay is blown into a shape, and then covered by stripes of blue and red enameled paint. It is then placed back into the mould again to be blown to the final shape. In the end, the opening and the bottom made of green enamel are attached to the body under heat.③ Enameled glass snuff bottle with a female portrait of the Qing Dynasty, 7.1cm in height, kept in the Palace Museum in Beijing. The snuff bottle is concise with a deltoid white body and light green lid. It is manufactured by the palace glass workshop of the Hall of Mental Civilization of the Qing Dynasty. Glassware-making reached its peak in Qing Dynasty. There were two centers of glass-making in China. One was in South China (Guangzhou)and the other was in North China (Yanshen Town). Guangzhou was not only an important place for producing domestic-made glassware, but also a center of imported foreign glassware. Glassware being made in Guangzhou was called”Guang-zhu.” It is light, thin and fragile, and few works could be seen nowadays. The most precious glassware of Yanshen Town was “Qing-Lian.” But the category of glassware has become more abundant. Most of them were utensils and ornaments with low practical value. In 1904, when Qing Dynasty promulgated its”new policies,”Hu Ting”gan, the Head of Shandong Province, established a glassware company in Boshan, and 7 German technicians were hired to make glassware. Since then, the western formula and crafts of making plate glass were introduced to China. Bronze Patterns of the Warring States Period, by Wang Jianzhong, 26x7x39cm, contemporary glass artwork. The work is repeatedly molded and fired. Every piece of the work is fired individually in the klin and then be put together to be fired in the klin. The patterns-resembling those of bronze wares from the Warring States Period-on the green glass are engraved by hand, rendering a decorous and ancient flavor. The first imperial glass factory of Qing Dynasty was built during the reign of Emperor Kangxi. Later, this factory was managed by the Glass Making Office affiliated to Imperial Household Department in Hall of Mental Cultivation, and was responsible for making glassware for the royal family. During the reign of Emperor Qianlong, the imperial glass factory reached its peak in terms of production scale, technological level variety and quantity of glassware. It was famous for combining the glass-making crafts of South and North China with those of western countries. The glassware produced in the imperial factory was extremely exquisite. They have vigorous, simple appearance, and represent the highest technological level of glassware-making in Qing Dynasty. Most utensils are bottles, furnaces, pots, bowls, cups, plates, vessels and snuff bottles, with more than 30 colors, such as white, red, dark-blue, light-blue and purple. Various methods were used to decorate these utensils, such as base-mixing, materials-sticking, gold-star materials and color enamel. “Materials-sticking”is the most important innovation on glass decoration in Qing Dynasty.
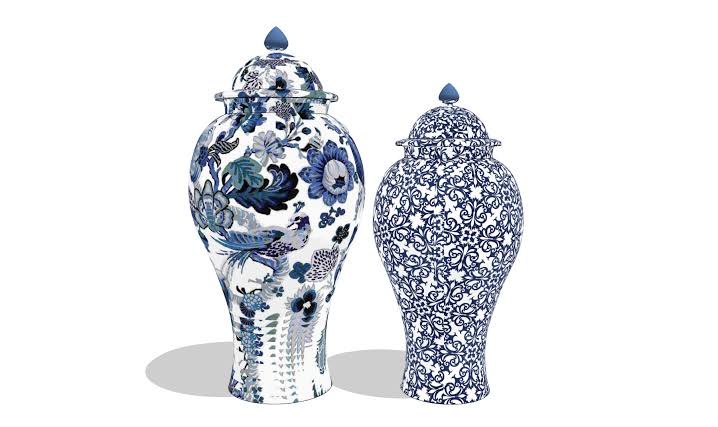
Craftsman would stick different patterns made of colored glass on white or colored glass bases, and then, polish the surface of glassware. Since the reign of Emperor Jiaqing, the imperial glass factory had been on the decline, and stopped making colored enamel glassware. Different from the declining imperial glass factory, privately-owned glass workshops were prosperous in Qing Dynasty. Snuff bottle was an important product of these workshops. Under the reign of Emperor Qianlong, workshops making snuff bottles already appeared in Beijing. The Xin Family, Le Family and Yuan Family were the most famous snuff bottle producers at that time. Interior painted snuff bottles were most popular during the reign of Emperor Guangxu and in early 20century. Craftsmen chose glass or crystal as the base of snuff bottle. They would take a bamboo stick, sharpen one end of it, and bend it, so as to make a thin, hooked bamboo pen. They would dip this pen in pigment and paint on the interior wall of the snuff bottle. The drawing techniques are diversified, including pastel, ink-painting, shallow deep red and strong-coloring. Some craftsmen imitated the artworks of famous Chinese artists. Others made reference from oil painting skills of western countries.
The contents of decoration were extensive. Under the influence of painting and photograph in late Qing Dynasty some craftsmen painted portraits on snuff bottles. Boshan in Shandong Province was an important production base of snuff bottles. Since the reign of Emperor Yongzheng and Emperor Qianlong, the sales volume of glass snuff bottle was high in China. Glassware-making became a prosperous business in Boshan. The “Lu Style”craftsmen use bamboo or willow brush to paint on the interior wall of snuff bottles. Their paintings have abundant appearance, delicate lines and smooth and fluent style. In Republic of China, the glassware-making business was prosperous in Beijing and Zibo in Shandong Province. However, the entire industry was on a decline due to the chaos caused by wars. Since the195s, the production scale of glassware was expanded. Glass factories were established in several places nationwide. Diversified utensils for daily use were produced by these factories. The crafts and categories of glassware became more abundant than before. Craftsmen in Beijing, Zobo and Henshui in Hebei Province inherited traditional painting crafts of interior painted snuff bottles, and formed three major styles: “Jing Style,” “Ji Style”and “Lu Style, and made this unique craft famous all over the world China also sent the first generation of students to study glass art in East Europe and introduce glassware art with decorative style to China. Since then, glass art was considered as plastic arts using special materials. Imitation of nature and symbolic presentation has become the theme of artists and glassware makers for a long time. Seven Intellectuals in a Bamboo Forest, by Zhou Gang in 2013, 70×30 x28cm. This crystal work is made by thermoplastic glass with the blowing technique. The figures of seven intellectuals are very lifelike Since the 1990s, contemporary Chinese glass art has both the identity of designing and art. In 2000, College of Fine Arts of Tsinghua University and College of Fines Arts of Shanghai University established the major of glass art at the same time. Later, major of glass art was gradually established in other universities in China. Glass is no longer a “raw material” in a conventional sense, but exists as a “media of creation. “It not only changed the methods of glass art creation, but also changed the people’s cognitive attitude towards glass art. Tracing the deposits of Chinese culture and exploring the boundary of modern art has become a new orientation of development of contemporary glass art. In 2014, the “1895 China Contemporary Applied Arts Exhibition& Academic Forum-China- Contemporary Glass Art Exhibition”raised the curtain in Nantong of Jiansu Province. Several masterpieces of glass art were displayed on the exhibition, such as”Vestige of the Warring States”by Wang Jianzhong, “Disappear” by Lin Xiaoyan and “Seven Sages in Bamboo Forest” by Zhou Gang. These artworks use glass as the material to express the artists’ cognitions on tradition and modern, nature and humanity, arts and imagination. The ever-changing performance nature of contemporary glass art, which crosses over manmade and naturally-evolved nature, attracts numerous painters, sculptors and ceramists to create artworks. Various crafts, such as die-casting, blowing and comprehensive molding, extend glass artworks to diversified fields. For example, in “Sunflowers,” a series of works created by Xu Jiang, the artist extends the sunflowers in oil painting to translucent glass sunflowers in sculptural forms. The changes of material and texture conveyed unique symbolic metaphor. Like other traditional crafts, such as jade-ware art, pottery art and lacquer-ware art, contemporary Chinese glass art is rejuvenating. Artists pay attention to the integration of materials and crafts, explore the conception of traditional Chinese art, express contemporary humanistic feelings, reveal modern artistic concepts and diversified development features.
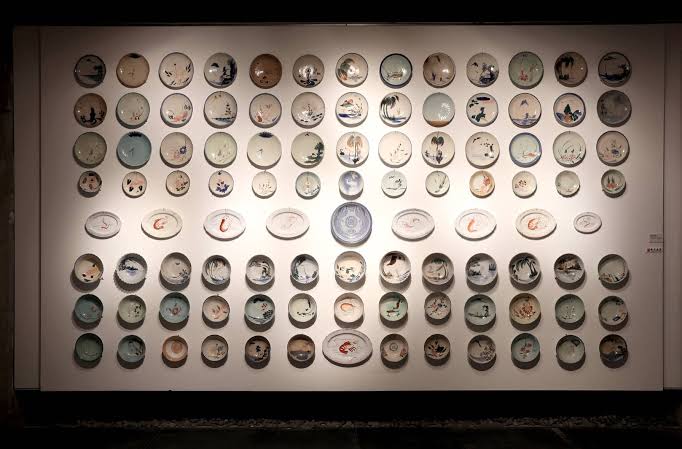