Chinese Printing and dyeing
13 min readChina has had a long history in dying textile fabrics with natural dyestuff extracted from minerals, plants and animals. Taking a comprehensive view of the development process of the printing and dyeing techniques in ancient China, there are three shifts noteworthy: first is the shift from natural mineral dyes to plant dyes; second is the shift from dyeing with primary color to combined color; and third is the shift from painting, sewing, stitching and incorporating the decorative patterns onto the fabrics to hand printing. As for dyes, although mineral dyes were adopted earlier, plant dyes are used more widely. Taking red color as an example, Chinese ancestors were able to use natural pigments for dyeing and decoration as early as the late neolithic period 4-5 thousand years ago. For example, hematite powder was used to dye the linen red; later cinnabar (mercuric sulfide) was used to dye the same color. However, these mineral dyes have poor fastness. In Zhou Dynasty, a significant breakthrough was made in the dyeing technique that mordant dyes and mordant were used, which dramatically enriched the variety of colors.
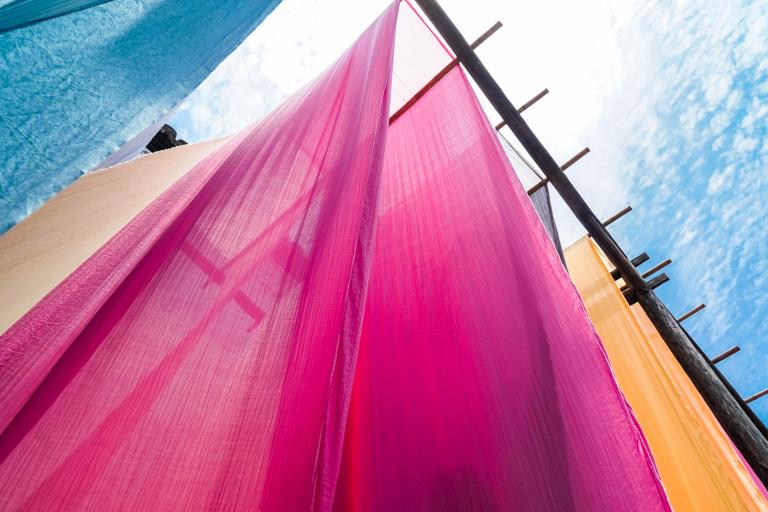
For example, alizarin contained in the root of madder was the main material to dye red, but it was hard to put color on the fibers without adding any mordant. If alum is used as the mordant, bright red can be put on the fibers. Taking blue as another example, people were able to take advantage of indigo plant to dye colors in the Xia Dynasty and conduct artificial cultivation by understanding the growth rule of the indigo plant. In the Spring and Autumn and Warring States Periods indigo plant was used to produce indigo to dye blue. As what is said in Xunzi: Encouraging Learning, blue comes from the indigo plant but is bluer than the plant itself. Plant dyes used then mainly included: madder, indigo plant, cape jasmine, cotinus coggygria, acorn, lithospermum and hispid arthraxon. As for the level of dyeing, the technique of combined dyeing of a far-reaching influence was created in the Zhou Dynasty immerse the fabrics into the containers containing dyes of one or multiple colors for several times successively to get similar colors of different shades or other new colors. The Book of Diverse Crafts, a monograph on crafts in the pre-Qin Period, describes the technique of combined dyeing in detail “Fabrics are dyed Xun if immersed for three times, Zou if immersed for five times and Zi after immersed for seven times, i.e. the fabrics are dyed Xun(dark red) if immersed in the red dyes for three times, Zou (light black with red) if continue to be immersed into black dyes twice, and Zi (dark black) after two more rounds of dip dyeing.
The dyeing industry of China has continued to use the combined color technique of multiple dip dyeing until modern times. Cotton cloth with dyed blue and white flowers of the Eastern Han Dynasty, 86cm in length, kept in the Xinjiang Uygur Autonomous Region Museum. On the bottom left is a figure of Buddha with chest exposed, hands holding a rhyton and a halo behind the head. Its original is supposed to be a larger decorative batik religious painting During the Spring and Autumn Period(70-475bc) and Warring States Period (475-221 BC), technology and management of vegetable dyeing, including category and collection of dye plants, dyeing process and the use of mordant, were already quite developed. According to Zhouli Tianguan (Rites of Zhou: Official of Heaven), there were professional positions such as ‘dyers’ and ‘dye plants regulators’ in the royal manual workshop in charge of silk dyeing for Zhou’s royal family. New colors were increasingly produced. To be specific, Shijing (The Book of Songs)mentioned various kinds of colors.
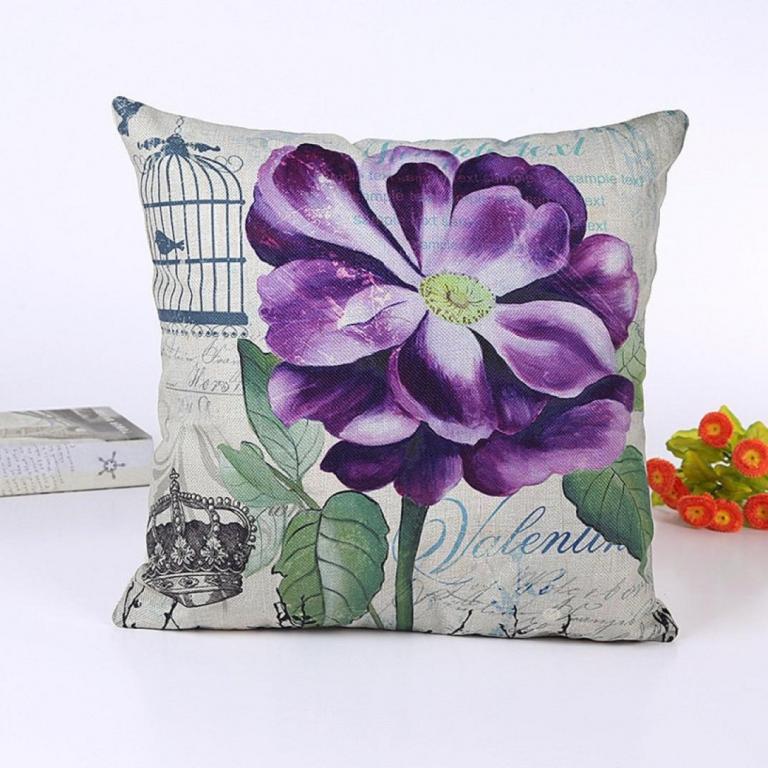
There were sentences such as “green coat with inner side yellow,””you worn a blue coat, “and “somewhere between black and yellow.” During Qin and Han dynasties, the scale and species of dye plants were significantly expanded. Vegetable dyeing was even under scale operation. And dyeing technology was also quite advanced. There were mainly two kinds of dyeing methods. First was to weave the silk before it got dyed, which applied to thin silk, leno, delicate silk and so on. Second method was to dye the threads before weaving, which applied to brocade for instance. Brocades with Chinese characters such as延年益寿(May you long live)and”万事如意(Wish you have all you want), which were unearthed in the tomb of Eastern Han Dynasty in Minfeng, Xinjiang province in1959, were made of silk threads of various colors such as crimson, white, yellow, brown, sapphire blue, light blue, bright green, reddish purple, light orange and light brown. This demonstrated the advanced dyeing technology and exquisite color scheme of that time. Shuowei Jiezi (Origin of Chinese Characters), a book written by Xu Shen of Eastern Han Dynasty, listed more than 39 kinds of colors of textiles, most of which were silk products. A part of the tie-dyed silk with a four-petal flower pattern and natural shades of colors of the Tang Dynasty, kept in the Xinjiang Uygur Autonomous Region Museum Two types of clip-dyed silk with patterns of linked circles, kept in the British Museum. The linked circles are filled with distinct and well-shaped flower patterns. The preparation of vegetable dyes was quite developed until Northern and Southern Dynasties (AD 420-589) that the vegetable dyes could be storied for use for a long period of time. Qimin Yaoshu, a book on agriculture written by Jia Sixie in Northern Wei Dynasty, initiated a detailed record of the operation method of the process for producing Dianlan(indigo blue)out of bluegrass.
After Northern and Southern Dynasties, various types of yellow dyes were found, including di huang, huaihua, huangbo, jianghuang, zhehuang. Silk products made from zhehuang appeared to be ochre yellow under the moon yet ochre red by candlelight. Because the color seemed quite dazzled, it was used for the clothes of the emperor since Sui Dynasty. When it got to Tang Dynasty, vegetable dyes developed into the dominant approach and technology of dyeing that was much more widely used than other natural dyestuff. And vegetable dyes were widely and skillfully used for producing silk. For instance, the colors of silk products of Tang Dynasty unearthed in Turfan, Xinjiang were as much as 24 different types. Rich and varied secondary colors were made by dyeing chromatically with the mastering of the method of original color dyeing methods. Wood-block color-printing clot x and peonies in Zhejiang, 1920s. Rolling-printing cover side of a quilt with a pattern of dancing peacock in Beijing, designed by Yang Shuping, cotton-based- machine printing,1960s The earliest exiting printed fabric was the silk quilt cover with printings unearthed in the tomb of Chu of Warring States Period in Changsha, Hunan. Silk products with printed patterns were found in Mawangdui of Changsha and in the tomb of Western Han Dynasty in Mozuizi, Wuwei, Gansu. Among them, Wen sha unearthed in Mawangdui, with silver white and bright yellow pattern and grey grounding, was chromatically printed with two relief printings, which demonstrated the ar extraordinary level of technology. Strangely however, this technology had never used in printed textiles for centuries since Western Han Dynasty.
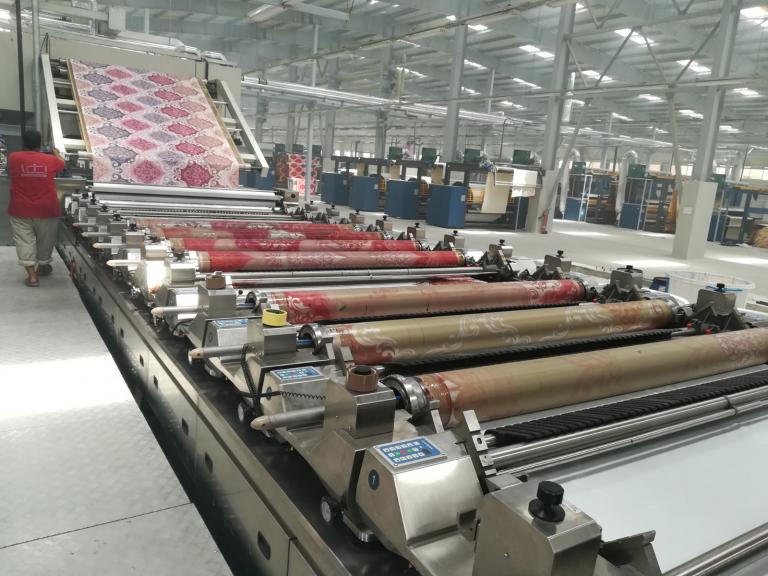
In central China, the renewed boom of printing technology started with figured silk fabrics (silk products with partial stenciling painting or dyeing-proof paintings). As a result, figured silk fabrics were used to refer to general painted silk products. When it got to Tang Dynasty, common fabric painting and dyeing processes included jiaoxie (tie dyeing), jiaxie (indigo dyeing), laxie (batik dyeing and huixie (alkaline dyeing).Jiaoxie is similar to modern zharan. It was also an ancient folk printing and dyeing process by tied dyeing. Based on specific pictures, jiaoxie was performed by knitting the textile into designed shapes with needles and threads, or by directly tying up with the threads, and next was to ensure that the fabrics were tied up tightly so as to make them gathered and overlapped. When dyeing, the overlapped parts would be scarcely dyed while other parts were appropriately dyed. In this way, the product appeared to have smudge effect with layered colors. Jiaoxie can make abstract and vague pictures and was quite easy to perform. It was widely used among the folk in Eastern Jin Dynasty. The existing earliest jiaoxie dyed products was jiaoxie dyed silk of Jin Dynasty unearthed in Astana ancient tomb in Xinjiang. The knitting traces and crinkles seemed vaguely visible even to this day. In Northern and Southern Dynasties, the famous “Lu Tai Zijie” and “Yuzijie” patterns were created. According to the dressing of unearthed dancer figurine of Sui Dynasty,”Lutaiwen”appeared to be jiaoxie dyed patterns of one single color or more with color as the background, white points as the pattern. Jiaoxie prevailed during the Sui Dynasty and Tang Dynasties. It is supposed that jiaxie was invented in the royal palace during the governance of Tangxuanzong. It spread outside of the palace and prevailed in the flouring period of Tang Dynasty. The procedure of jiaxie was to clamp the folded cloth with two boards of uniform carved patterns and then to dye both sides of the boards. In this way, the pattern was distinct and symmetrical To repeatedly perform dyeing will result in exquisite products. In Tang dynasty, jiaxie was not only used for clothes of women but also for furniture decoration, jiaxie dyed screens for example. There was another method for jiaxie in Tang Dynasty, which was to process the warp by jiaoxie in the first place, and then to weave patterns for the products. Each thread had varied tension resulted from tie dyeing, and the shape of the pattern also tended to be varied when weaving, which resulted in the special artistic charm of the products. Modern printed fabrics derived from dyed fabrics of Tang Dynasty. The process was to casually weave the warp (which means to make the warp loosely weaved)on the spinning machines, then to print patterns on it.
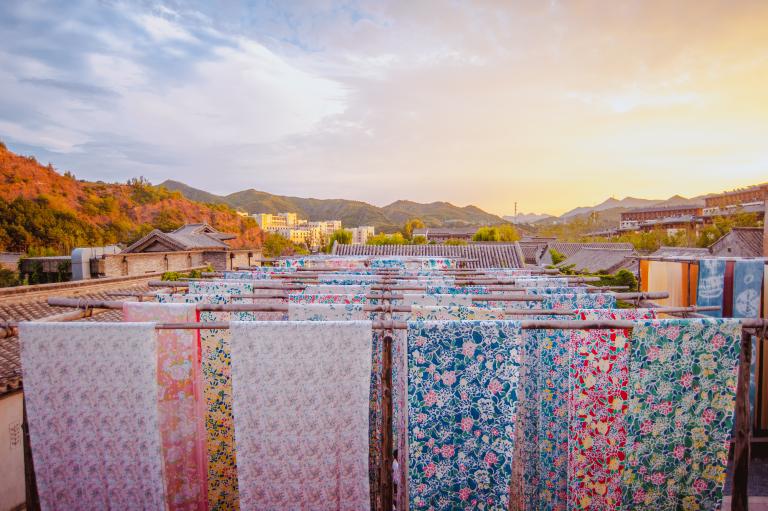
Next step was to dismantle the loosely weaved warp and to normally weave once again. In this way, the product appeared to have unique charm. Laxie was also known as wax dyeing, which implies “preventing being dyed by wax” as a matter of fact. The procedure of laxie was to draw pictures with wax on natural fabrics such as flax, silk, cotton, fur, and then to dye the fabrics. Immersed into the fabrics, the wax had water-proof effect and kept the dye outside. After removing the wax by boiling water, white patterns can be created. Solidification and shrinkage of wax will normally result in many natural cracks. And after dyeing, there will be some unique and natural texture on the product. As an ancient dyeing-resisting process of China, wax dyeing had a quite long history As early as Qin Dynasty and Han Dynasty, ancestors of some ethnic groups, such as Miao, Yao, Buyi, had already mastered the technology of wax dyeing.Bouyei ethnic-style batik lace of the Qing Dynasty, 29cm in length, kept in the Nationalities Museum, Minzu University of China.
It is hand-made by Bouyei people in Guizhou Province, and wax printed by traditional manual approach. It is generally used for sewing cuffs and sleeves and decorative purposes. In Tang Dynasty, there was a special alkaline printing craft for silk, referred to as “Hui Xie, “which used alkaline mordant like soy flour, lime, plant ash to make resist printing. It was a kind of traditional pierced white pulp resist-printing, whose craft was similar to today’s’ blue calico. In the end of the13 century, handmade cotton -spinning technology has been widely spread in Jiangsu and Anhui, Jiangsu and Zhejiang, where Hui Xie was exclusively used in cotton printing and dyeing, thus the craft of blue calico became popular in regions south of Yangtze River. Blue calico used indigo as its dye and hand-spun cotton as its raw material, and was made through several procedures like block-cutting, oil-applying, resistant-mixing (making pulp from mixing resistant together), pulp-applying dyeing, drying, pulp-powder-removing. Traditional blue calico is featured with four characteristics: (1) the use of local materials and low production cost, as a cut block is available for many years; (2)simple processing procedures with flexible links facilitating moving and cleaning; (3)durable, breathable and high-quality cloth, brightly colored patterns; (4) anti-moth and mildew-proof.
Blue calico is typically in two forms-blue cloth with white patterns and white cloth with blue patterns, which has been passed on ever since. Household items like bed nets, quilt covers, baggage, scarves and curtains made of blue calico are simple and classic with bright color and cultured patterns. In 17century, Songjiang cloth was prevailed in Britain for its stable beautiful color even after washed for many times. Since the Qing Dynasty, the craft of blue calico has been developed rapidly, and blue calico was produced into dyehouses in different places. Famous places of origin were Jiaxing in Zhejiang, Suzhou and Nantong in Jiangsu, Changde in Hunan, Tianmen in Hubei, Chengdu in Sichuan, etc. Fan-dyed wall decoration with animal patterns, designed by Chai Fei, 1960s Wood-block printing wall cloth in Xinjiang, cotton-based hand printing, 1950s. During the period of Ming and Qing Dynasty, vegetable dyes were not only self -sufficient, but also exported in great volume. At that time, the application and technology in planting, preparation and dyeing has come into its flourishing period and dyehouses have also been greatly developed. Meanwhile, the advancement of woodblock printing technology promoted the development of color-topping and printing technology in woodblock, paper-block and tulle-printing. All kinds of silk textiles in Ming and Qing Dynasty (raw silk was spun based on given patterns after preliminary degumming and dyeing) were famous for their gorgeous color which not only displayed exquisite embroidery craft, but also reflected superb skills in colored scouring and printing. Qing government was equipped with Zhiran Bureau, and there was Dianlan Center in regions south of the Yangtze River, which also showed the high level of printing technology. Besides, dyehouse business once was a significant and flourished local industry. Before Perot printing machine was invented in France in 1834, Chinese hand -dyeing craft was always a focus of worldwide attentions. In early 2000s, foreign machine-made calico surged up in Chinese market, and revealed its advantage in the competition, which has caused declining of folk homespun and calico production in coastal areas.
On the basis of blue calico, colored calico emerged in provinces in Northern China like Hebei, Henan, Shandong, Shanxi and Shaanxi, but was less developed due to the impact of machine-made calico. based on traditional dyehouses, while the process involved the whole dyeing and During the period of the Republic of China, Chinese printing industry was mainly finishing procedures. Traditional dyehouses, scattered in numerous small towns, usually used self-grind natural dyestuff Since the chemical dye imported, many dyehouses gradually increased the use of chemical dyes, and then modern dyeing factories gradually replaced the traditional craft production. Moreover, scouring and bleaching businesses for cotton products in some cities have gradually developed from manual operation to mechanized steamy scouring. Procedures like singeing, desizing, high-pressure scouring, mercerizing and bleaching were successively established, while auxiliaries like soda ash, caustic soda and bleaching powder were also introduced. During the times of the Republic of China, Traditional dyehouses were further divided into bleaching workshops, printing workshops and cloth-rolling workshops out of the need for specialization. “Cloth-rolling workshops”were specialized in inishing cotton cloth. Cloth-rolling craft, also known as calendering, mainly engaged in using the smooth surface of stones to crush on the fabric after it was pasted, so that the cloth cover could became smother and cleaner, which made printing and dyeing easier. As for printing, the old and new methods coexisted. Folk craft like batik, tie-dyeing was kept; meanwhile, hand printing gradually integrated the use of paper or rubber pierced-blocks. Besides, gray-printing workshops made blue and white printed products through resist printing, while color-printing workshops produced colorful products through watermark method.
Since 1930s, China has started to independently produce part of the dyeing and finishing equipments and chemical dyes. Transfer-printing decorative cloth in Shanghai, designed by Yang Dongqi, chemical fiber hot-press printing, 1995 After 1949, dyeing and weaving techniques have changed rapidly, and textile raw materials further included various chemical fibers besides natural fibers like cotton, silk wool and linen. Modern printing and dyeing techniques like roller printing, screen printing, rotary screen printing and transfer printing became the mainstream in large -scale production. Those techniques not only improved the yield and quality of printing products, but also provided a broader platform to show the printed design. In addition, burnt-out and hand-painted craft has also added splendor to modern printing technology. Modern calico has diversified patterns and rich colors, and it features in its simple and fresh style When traditional printing technology encounters contemporary design thinking, various artistic effects emerge, including three -dimensional effect, velvet-like and brocade-like effect. Folk printing and dyeing crafts can be found in every corner of China, especially in some dwelling areas of ethnic minorities and relatively remote areas, where traditional weaving and dyeing practices are still retained.
For example, there are batik of the Miao and Buyi nationality in Guizhou, tie-dyeing and Zhuang Brocade of the Zhuang nationality in Guangxi, Tujia Brocade in Xiangxi autonomous prefecture of Hunan, Li Brocade of the Li nationality in Hainan cotton cloth of the Dong nationality, Atlas Silk of Uygur, and blue calico of the Han nationality which are all beautiful products with strong and distinctive ethnic flavor. Machine dyeing craft can never be comparable to traditional hand-dyeing craft in terms of the natural non-artificial texture, unique color-applying method and decorative artistic effect, which make the traditional craft one of the Chinese folk art treasures. Display The display plays an important role in the residence environment in China, and the unique display art and system have taken shape. Display articles are of both practical and artistic values, and even manifest the personality ideal, aesthetic spirit and life fun of Chinese people. Furniture is the essential indoor functional display. Chinese furniture was originally short, but then taller. It was not until the Song and Yuan dynasties that furniture was generally tall and customized according to the figure of different users. The Ming-style- furniture stands out for its particular aterials and superb workmanship, embodying the aesthetic taste of pursuing the simple and unsophisticated and the elegant thing. Craftsmanshi and formative art of Ming-style furniture is handed down to present, and still an element in modern furniture. Gold and silver ware, glassware, and enamel ware are long-standing and well-established. Although they are not the typical traditional Chinese handicraft, in contrast with Western display articles, they stand out in the shape, texture, and color, and are the crystallization of cultures and customs of many ethnical groups. Their aesthetic charm is a new splendor for modern craftsmanship concept. Bamboo carving, wood carving, ivory and horn carving, the miscellaneous craftsmanship in China, found their heyday in Ming and Qing dynasties, falling into practical and display articles, from dailvessels to stationary and to toys, just about everything you could wish for. The craftsmanship can be classified into circular engravure, deep and shallow relief, and hollow engraving, with collage and inlay sometimes added. Despite being mostly small wares, they are elaborate and exquisite, and the indispensable display articles for adding interest to life, and presentation of the love for life and aesthetic taste of Chinese nation.
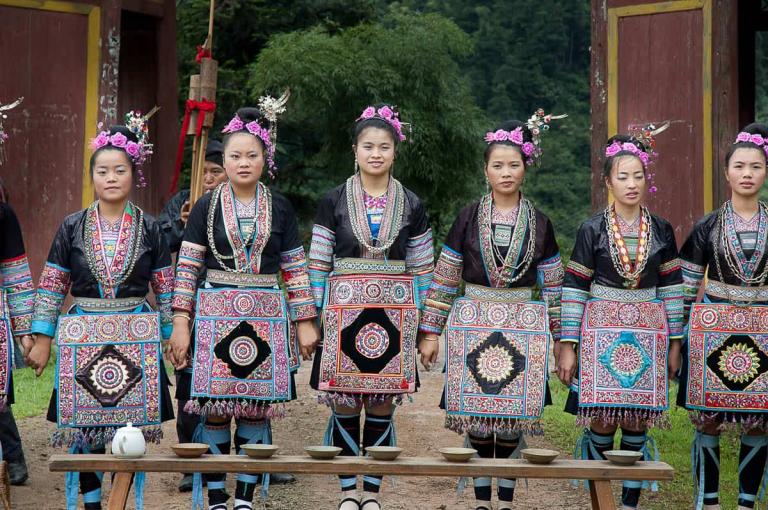